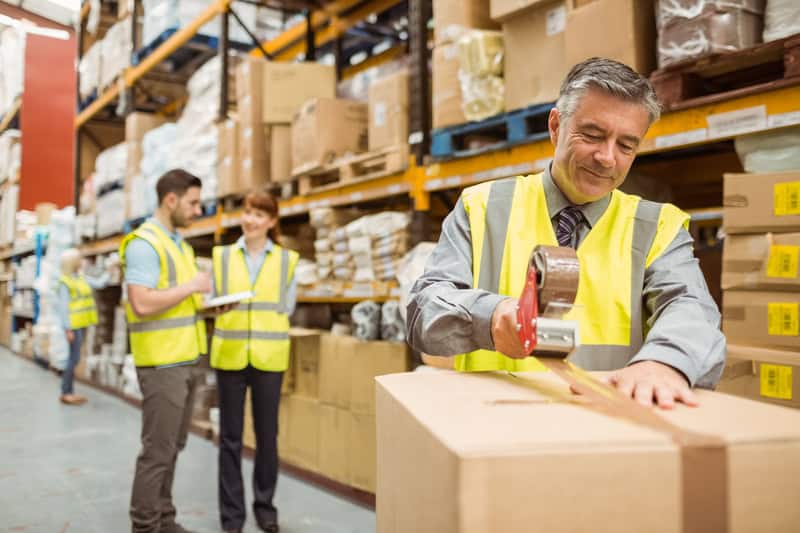
Root Cause Analysis With CAPA
This highly effective Root Cause Analysis with CAPA workshop instills the basics on how to use a simple, yet proven approach to correcting and preventing problems or nonconformities that exist anywhere in the organization.
Root Cause Analysis With CAPA
This course discusses the philosophy, problem solving approaches, continuous improvement and more. This training can help lead to establishing procedures that satisfy quality management requirements for establishing a system for corrective action.
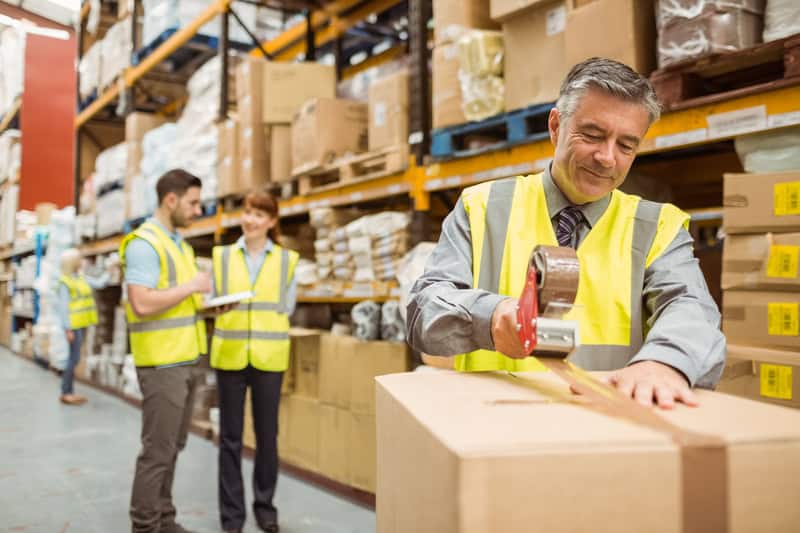
Course Objectives
- Discuss the philosophy, problem solving approaches, continuous improvement, and more
- Driving improvement through Corrective Action, Preventative Action, and problem solving.
- Key components to helping organizations understand how to achieve results that “stay” in place.
- Orientation to ISO9001:2015 for both those learning about this baseline business standard (and its approach to continuous improvement, management focus, and customer satisfaction) and for those in industries regulated by the standard or one of its derivatives.
- Key components to helping organizations understand how to achieve results that “stay” in place.
- Orientation to ISO9001:2015 for both those learning about this baseline business standard (and its approach to continuous improvement, management focus, and customer satisfaction) and for those in industries regulated by the standard or one of its derivatives.
Target Audience
- Professionals at all levels seeking a continuous improvement process
- Individuals focused on correcting past problems and preventing future issues
- Employees in regulated industries requiring compliance with industry standards
Agenda
- Lean and Quality
- Philosophy (Brief)
- Total Quality Management
- Crosby’s Steps to Quality Improvement
- Deming’s 14 Point Plan
- Corrective Action Process
- Risk Assessment(former Preventative Action) Process
- Difference between CA and Risk Assessment/ PA
- ISO 9001:2015 CA/Risk Assessment/PA and Improvement Requirements and Implementation
- Problem Solving Approach – Overview
- Fishbone Diagram, Pareto Chart, Check Sheets, Control and Attribute Charts, Flowcharts, Histograms, Scatter Diagrams, Benchmarking
- Design of Experiments
- FMEA’s (Risk Assessment Tool)
- Teams
- Continuous Improvement
- Root Cause Analysis
- Importance of Finding Root Cause
- Benefits of Eliminating the Root Cause
- Finding the Root Cause
- What does a good RCA look like?
- Root Cause and CA/Risk Assessment/PA
- 8D Approach
- 5 Why’s
- RCA Examples
- Cost of Poor Quality Overview
Course Delivery
- In-Person Training
- Online Self-Paced
- Training for Teams
- Virtual Live Training
Prerequisites
- None